OEM/ODM Supplier Optical Fiber Tight Buffer Production Line - Cable stranded cable production line – GELD
Short Description:
Product Detail
Product Tags
Related Video
Feedback (2)
OEM/ODM Supplier Optical Fiber Tight Buffer Production Line - Cable stranded cable production line – GELD Detail:
Optical cable maximum diameter | Ф25mm |
buffer tuber diameter / quantity | Ф1.5~Ф3.0mm/12 |
Structural speed | 100m/min |
Typical production speed | 90m/min(tie pitch 65mm, tie pitch 25mm./(Speed is related to cable pitch and reverse Angle) |
Cable pitch (single helix) | 55~1000mm±5mm |
SZ stranding Angle | ±12π~±16π |
Maximum rotational speed of tie yarn head | 4000rpm |
Tie yarn section distance | 20~50mm |
Meter accuracy | ≤2‰ |
added losses | ≤0.02dB/km |
Device color | Color of mechanical part: RAL5015/Electrical part color: RAL 7032/Rotated part color: RAL 2003 |
Direction of equipment | Left to put right |
1. | PN1250 reinforced core cable tray |
1PC |
2. | Φ800mm storage line type laying out speed controller |
1PC |
3. | Steel wire gripper |
1PC |
4. | Steel bracket |
3PC |
5. | Steel wire paste filling device (customer’s own) |
1PC |
6. | PN800mm beam tube active laying out device (including pendulum rod dance wheel) |
12PCS |
7. | Differential type SZ stranded unit |
1PC |
8. | Double-disc concentric yarn binding device |
1PC |
9. | Cable core oil paste filling device |
1PC |
10. | Single plate concentric yarn machine + longitudinal package integrated machine |
1PC |
11. | Φ800mm twin-wheel tractor |
1PC |
12. | Φ800mm storage speed controller |
1PC |
13. | PN1000mm~PN1850mm gantry rail line frame |
1PC |
14. | Electric control system |
1PC |
15. | Equipment connecting cables and wire chlots |
1SET |
PN1250 reinforced core cable tray
Electric lifting, clamping, AC AC motor and Danfoss inverter to control the discharge speed and traction synchronization, there is an independent electric control box, the operation station panel is set at the height and position of easy operation;
The wiring frame fully considers the humanized operation, and the single person can complete the operation of the upper and lower plate tools independently.
The wiring frame adopts the top structure, with lifting, clamping overload insurance, limit position insurance, working state self-locking and other functions.
payoff tension: 50~150N
Specification of disk: PN800~PN1250mm
Maximum weight of cable tray: 2T
Minimum closing distance: 460mm
Shaft hole diameter of releasing disc: 80mm
Steel wire gripper
Air pressure can be adjusted manually
Shut down automatically tighten up, start up automatically release
The release and tightening can be controlled by manual button.
Steel bracket
Ф800mm storage line type releasing speed controller
Double wheel line storage type, PID control, pre-tensioning, laying out process, maintain constant tension, constant position.
The tension is given by the cylinder, and the potentiometer feedback the speed change, so that the cable core release speed and traction speed are automatically synchronized;
take up pulley: Ф800 mm*4pcs
Tension control range: 50~300N
The extreme position of both ends of the slide table is equipped with travel switches.
Steel wire paste filling device (customer’s own)
The supplier is responsible for the integration
PN800mm disc casing release device (including swing rod type dance wheel)
Portal frame structure, swing bar tension controller. Active wire release, Danvers frequency conversion speed regulation.
Dance wheel and transition wheel: multi-turn light ABS regulating wheel, and the path has a reliable anti-casing jump limit device.
Under normal speed, the bushing cable tray runs smoothly, and the dancer is in a stable state without great fluctuation.
The status of each cable tray can be displayed on the main control screen (green is the working state, red is the alarm state, and white is the unselected state).
The casing is set up with upper and lower alarm devices, and the alarm state will be displayed on the screen after the alarm. Meanwhile, the production line can automatically stop and protect the casing and cable core.
The guide wheel and dance wheel are made of plastic with light weight and low friction resistance.
12 casing cable tray with manual control of forward and reverse.
The casing routing path is equipped with sufficient ceramic guide ring and casing path protection parts, on the one hand, to ensure the smooth path of the casing, small resistance, on the other hand, to ensure the casing in high-speed production of stable routing, not easy to jump out of the path.
The casing drawout tension can be adjusted continuously and conveniently from 1.0N to 10N, while leaving enough area on the drawout rack for tension marking.
Casing disc size: Flange diameter is 800mm, disc width is 600mm, center hole is 80mm
Loose casing diameter: Ф1.2~Ф3.5mm
pay-off speed: 100m/min
Top diameter: Ф80mm
Range of wire tension: 1.0~10N
Maximum load of cable tray: 200KG
SZ stranding unit (differential)
A3 steel welding frame, A3 steel + Plexiglass protective cover (opening and closing Angle ≥90°)
Multi motor differential twisted disc twisted tube, stainless steel central tube.
4 Motor structure (3KW+3KW+2KW+2KW), Panasonic AC servo motor drive.
The stranded pipe structure is 1+12, and one set of character cable stranded pipe is provided (Party A shall provide pictures for reference).
TURNS: 5~8pcs
Diameter of bushing Ф5mm, with porcelain ring.
Ф16mm strengthening core aperture, with porcelain ring
ange of stranded pitch: 55~300±3mm
The state of the stranding unit can be displayed on the main control screen (green is the working state, red is the alarm state, white is the unselected state)
The hinge pitch is stable, that is, the pitch is consistent in the stages of increasing speed, decreasing speed and constant speed under the production speed that can be met by the equipment.
Double disc concentric yarn binding device
Two tie ends rotating in opposite directions. Vehicle structure.
A3 steel welding frame, A3 steel + Plexiglas protective cover (opening and closing Angle ≥90°), gas spring assisted opening and closing.
0.75KW Panasonic AC servo motor drives the yarn mass to release yarn at high speed, and 1KW Panasonic AC servo motor drives the aircraft to control the release tension.
Prepare yarn deposit: Each 1 regiment
The size of the yarn: Ф220mm×Ф94mm×190~216mm(D×d×L)
Tie yarn section distance: 20~40mm±3mm
Tie yarn tension: 2~10N
During a quick shutdown, the yarn will not tie the casing.
When fast shutdown, the yarn will not fly yarn winding.
No matter more yarn, less yarn, or slow, rise and uniform stage, the yarn tension is constant.
The status of yarn unit can be displayed on the main control screen (green is working, red is alarm, and white is unselected)
The real value of the yarn tension is consistent with the set value, and the tension can be adjusted continuously.
The same point of the yarn, and the position of the yarn point can be adjusted, through the yarn path smooth without burr
The yarn pitch is stable.
After the yarn is formed, the cable surface has hairyarn.
Cable core oil paste filling device
Standard cold filling system, equipped with a one-stage pneumatic diaphragm pump.
Fill the cable core with the ointment pressure.
The filling ointment is drawn from the rubber bucket to provide a certain outlet pressure to the filling pump to realize the filling of the reinforcing core.
Automatic oil filling paste is achieved by the liquid level pressure sensor.
Single disc concentric yarn machine + longitudinal package machine (water belt molding mold)
A3 steel welding frame, A3 steel + plexiglas shield (opening and closing angle 90), air spring auxiliary opening and closing.
0.75KW Panasonic AC servo motor drive yarn ball high speed yarn, 1KW Panasonic AC servo motor driven aircraft control yarn tension.
Spare yarn storage rack: 1PC
The size of the yarn: Ф220mm×Ф94mm×190~216mm(D×d×L)
Tie yarn section distance: 20~40mm±3mm
Tie yarn tension: 2~10N
During a quick shutdown, the yarn will not tie the casing.
When fast shutdown, the yarn will not fly yarn winding.
No matter more yarn, less yarn, or slow, rise and uniform stage, the yarn tension is constant.
The status of yarn unit can be displayed on the main control screen (green is working, red is alarm, and white is unselected)
The real value of the yarn tension is consistent with the set value, and the tension can be adjusted continuously.
The yarn pitch is stable.
After the yarn is formed, the cable surface has hairyarn.
The tension is controlled by the magnetic powder brake and can be adjusted by hand.
With broken belt alarm and residual alarm device.
Plate loading structure: pneumatic expansion shaft (Φ 76mm).
Bash width: 20~80mm
Pack bucket diameter: ≤Ф450mm
Belt and bucket length: ≤500
Pack barrel shaft hole: Ф76mm
Relay belt tension: 2N~8N
Φ800 mm double-wheel traction traction device + meter meter
A3 carbon steel welded box type structure, equipped with plexiglass visual protective door.
The main traction wheel has a 90 degree package Angle pressure cable belt, which reduces the belt slip rate and meter meter error.
Two Ф 800 cast metal slot wheels, one Ф 800 cast metal flat wheels.
Traction belt with cable core compression function, belt pack angle 90. The traction belt can be adjusted by air pressure, and when the line reinforcement core tension is maximum, the tension force ensures the stable operation of the equipment.
mmTraction wheel diameter is Φ800 mm
Maximum traction speed: 100m/min
tractive effort: 200KG
Drive motor: 5.5KW AC frequency conversion motor + reducer
Brake device: Equipped with disc brake function
meters counting accuracy: ≤2‰
Meter accuracy, there is a meter coefficient on the display can be corrected meter accuracy.
Ф800 mm storage line type receiving line speed control device
Double-wheel storage line type, PID control, line closing process, maintain a constant position.
Tension is given through the cylinder, the potentiometer feedback speed change, so that the cable core receiving speed and traction speed automatically synchronization;
Diameter of tension wheel: Ф800mm;4PCS
Tension control range: 50~300N
The stroke switch is installed at the limit position at both ends of the slide table.
PN1000~PN1850mm gantry rail line frame
The gantry underground rail structure is adopted.
Electric clamp and lifting are driven by the AC motor respectively.
Denver frequency conversion controller controls AC motor drive coil wiring. Denver converter controller controls AC motor wiring, with independent electric control button station,
Lift and clamping with wire bar protection device. Set the manual winding and winding functions:
Wire disk specifications: PN1000~PN1850
Terminal structure speed: 100m/min;
Layout distance: 5~30mm;
Carrying capacity: 4T
Lift, clamping and tension adjustment are installed beside the wiring frame. When the production line works, the lifting and clamp buttons do not work, and they are equipped with mobile operation panel; there are upper and lower safety limit and protection; plate clamp protection switch, and the plate has a certain pre-tightening force, and will not break the plate.
Electrical control system
The whole machine adopts the control technology of industrial computer and programmable controller (that is, PC + PLC) to realize synchronous operation of whole line and independent operation; production operation, parameter setting and display through production control machine, signal setting and motor speed are collected by PLC-S7-1200, data transmission between industrial controller and PLC through communication port, alarm display, and display frame are installed in the electric control cabinet. PLC (programmable controller) adopts Siemens S7 series products, product reliable operation; AC frequency conversion controller adopts DANFOSS series products; AC servo controller adopts imported products (Panasonic); air switch, contact electrical adopts joint venture Schneider products; electric control cabinet with chassis at the bottom, power supply according to three phases and five lines;
All grounding wires and housing of the equipment have reliable grounding, with inverted cable function.
The communication between the industrial control machine and the PLC is conducted through the adapter, and the collection of digital quantity and analog quantity is realized through the input channel of PLC. After PLC CUP operation and processing, the switching quantity and analog quantity output channel of PLC are output to control the process of the whole production line. The industrial control machine provides a friendly man-machine interface for the operator to communicate with the PLC model, the parameters input by the operator to the PLC, provide the process data required for PLC operation, and send the PLC collected data to the industrial control machine enabling the operator to understand the state of the production line.
The man-machine interface has multiple interfaces, including control interface, parameter setting interface, alarm interface, event record and curve record, which can set, display and record the process parameters and states of the production line in real time. Each part can be controlled by centralized linkage or single movement control. All important process parameters in production can be saved, copied and printed to facilitate any failure during normal production, the alarm can be stopped immediately, and the specific alarm parts can be displayed on the alarm interface.。
The set process parameters are mainly: production speed, product length, yarn pitch, twisted pitch, stranded Angle, yarn tension, etc.;
The displayed process parameters mainly include: the actual production speed, product length, etc.;
The main alarm is: broken yarn alarm, broken strip alarm, line breaking upper limit, line breaking breaking, SZ twisted and twisted, each driver alarm, etc.;
Save the process parameters: product length, yarn pitch, stranded pitch, stranded angle, yarn tension, etc.;
The electric control cabinet adopts the three-phase and five-line system, all the devices are reliably grounded, the key parts have the safety protection function, and has the brake device;
Low-voltage electrical appliances using the domestic joint venture factory production brand. Electrical installation complies with IEC international standards;
Emergency stop switch at receiving, laying out, casing laying rack, winding platform and yarn machine;
All software and programs of the production line provide backup (original program);
Equipment connecting cables and overhead wire chlots
The supplier shall provide the cable and the overhead line trough for the equipment connection in the production line.
Main power supply incoming cable shall be provided by the Demander.
Equipment operation manual and operation manual, the premise of commissioning to provide the demander;
The basic diagram of the shape of the equipment;
The electrical principle and wiring diagram of the equipment (the actual wiring is consistent with the line number and the control system);
Mold Drawing
Transmission and lubrication drawings;
Certificate and date of delivery of outsourced components (including computer mainframe);
Parts and details of installation and maintenance;
A guide to the operation and maintenance of the equipment and a description of the purchased parts;
Provide necessary mechanical drawings according to equipment condition;
Supply of purchased spare parts and self-made spare parts, tools (including models, drawings, preferential prices of manufacturers and suppliers);
Provide the equipment wearing parts table.
Equipment safety standards: Production equipment in line with the relevant national equipment safety standards. The exterior of the device is marked with safety warning labels (for example, high voltage and rotation). The whole production line has reliable grounding protection, and the mechanical rotating part has reliable protective cover.
After the completion of the equipment, notify the demander to the supplier to participate in the preliminary inspection of the equipment (inspection of the appearance and basic performance of the equipment, without online debugging); The Demander shall conduct inspection according to the technical requirements table, production line equipment configuration table and other contents, and conduct preliminary acceptance according to process operation, equipment maintenance, structural rationality and safety.
Product detail pictures:
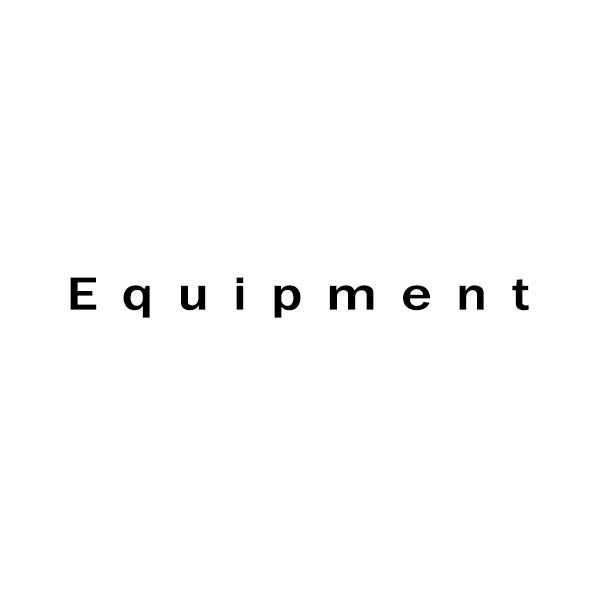
Related Product Guide:
With advanced technologies and facilities, strict high-quality handle, reasonable rate, superior services and close co-operation with prospects, we are devoted to furnishing the lower price for our customers for OEM/ODM Supplier Optical Fiber Tight Buffer Production Line - Cable stranded cable production line – GELD , The product will supply to all over the world, such as: Pakistan, Gambia, Belize, We also have the strong ability of integration to supply our whole heartedly service, and plan to build the warehouse in the different countries around the world, that will be more conveniently to service our customers.

The goods are very perfect and the company sales manager is warmful, we will come to this company to purchase next time.

Products categories
-
Fiber Optic Patch Cord Outdoor Optical cable c...
-
Quality Inspection for loose tube fiber - Aram...
-
PriceList for types of optical fiber - Non-con...
-
professional factory for “Optical Cable M...
-
factory low price Fustion Splice Tube - Adjust...
-
2022 High quality Three Bolt Guy Clamp - Three...